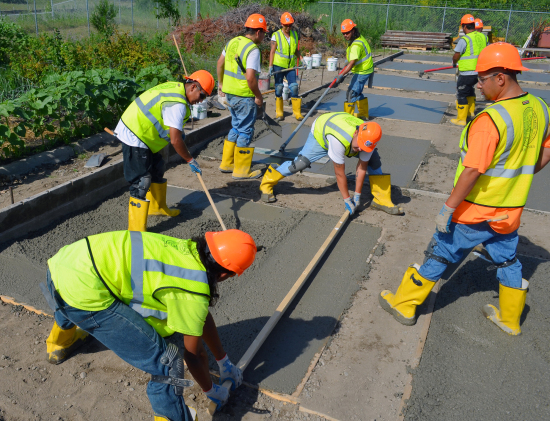
Share
As the first trickle of mud oozed out of the concrete truck’s chute, 13 trainees dressed in hardhats, safety vests and tall rubber boots sprung into action, using shovels and trowels to distribute the concrete evenly across 13 rectangular slabs.
The July heat was pushing 90 degrees, and the trainees, participants in a unique pre-apprenticeship program co-sponsored by the Cement Masons and area tribal authorities, worked in silence, heads down, as their instructors barked orders and critiqued their work.
“Let’s go, you’ve got to pick up the pace,” Local 633 apprenticeship instructor Moke Eaglefeathers warned three trainees as they leveled and smoothed one of the slabs. “Those guys over there are waiting on you. You’re falling behind.”
Concrete, any cement mason will tell you, is a perishable product. The brighter the sun, the shorter the lifespan. And the trainees, working on their final project of the program, wouldn’t get more than one shot to do the job right.
“Guys, this is the real world here. This is how fast it moves,” Local 633 instructor Dave Schutta said. “We’re not trying to bury you, but this is just it. This is the real deal.”
Two days later, all 13 trainees – 11 men and two women – were back at the Local 633 training center in New Brighton. They had traded the boots and vests for more formal attire, and their friends and family members, tribal leaders and dignitaries from MnDOT and the state Department of Labor had gathered to watch them take one big step closer to working, as Schutta put it, in the real world.
They’d made it to graduation.
“They went through 12 weeks of hell,” Eaglefeathers said. “I’m pretty hard on them, and I do it on purpose. If they can handle me, they can handle any supervisor or foreman out there.”
A member of the Cheyenne Tribe from Montana, Eaglefeathers calls Local 633’s pre-apprenticeship program “his baby.” He began reaching out to tribal authorities in Minnesota and Wisconsin six years ago after growing “tired of hearing about how there were no skilled workers on the reservations,” he said.
Since then Local 633 has graduated four classes of pre-apprentices, thanks to funding support from the Tribal Employment Rights Office (TERO) and public agencies, currently MnDOT. The most recent graduates included members of the Bois Forte Band of Chippewa, the Ho-Chunk Nation, the Red Lake Nation and the Leech Lake and Mille Lacs Ojibwe bands.
State Labor Commissioner Ken Peterson said programs like the Cement Masons’ are critical to making the construction trades workforce more reflective of the state’s broader demographics. Jobs in the trades used to be “reserved” for white males, but “things have changed a lot,” Peterson said. Now, apprenticeship programs statewide are creeping up on 20 percent women and minority participation. “And there’s still room to grow.”
On reservations where families struggle with unemployment, poverty, gang membership and other challenges, the training program offers a social benefit as well.
“You guys are going to be working in our communities, and you’re going to stabilize your families, stabilize your communities,” Bois Forte representative Ray Toutloff told graduates. “You’re all role models.”
Indeed, not everyone who started Local 633’s training program in late April made it to graduation 12 weeks later. Schutta and Eaglefeathers say they run the program like a jobsite, with strict rules about attendance and no tolerance for tardiness.
“When we do tool-recognition training, the first tool we bring out on the table is an alarm clock,” Schutta said. “The second is a backup battery.”
In addition to the “soft skills” necessary for employment, Local 633’s curriculum includes flat work, paving, curb-and-gutter technique, patching and decorative work – “skills that we’ll use for a lifetime,” according to Jasmine Funmaker, a graduate from the Ho-Chunk Nation.
Picking up the craft took determination and patience, said Bois Forte member Alexa Goodsky, who left her job as a housekeeper at Fortune Bay hotel and casino to enroll in the training.
“It started getting progressively easier, and what I’m supposed to do got clearer as time went on,” Goodsky said. “Every time we pour, I’ve learned something new and gotten better.”
Goodsky’s sister graduated from the Cement Mason’s program last year and has been working in the field with JE Dunn Construction ever since. Hers is just one of several success stories that indicate graduates of the program are in high demand.
“These people can go out next Monday and fit right in on a jobsite, as opposed to somebody coming in off the street and filling out an application with no experience,” Schutta said.
Several even decide to continue their training as union apprentices.
“We show them the basics here,” Eaglefeathers said. “We show them the necessary work ethic. If they don’t want to be a concrete finisher, we’re fine with that. We’ll open the door for them to go into another trade so they can have a good life and provide for their families.
“Union life has that pension, that security, that pride. Like any Native American out there, I have pride, and I also have union pride. We show them that. We show them that going union is the best way to work.”